Alnico is a cast or sintered alloy consisting primarily of iron, aluminum, nickel, cobalt, with minor amounts of other elements including copper and titanium. Alnico is produced by conventional foundry methods using resin bonded sand molds or powder metal manufacturing methods. Alnico is suitable for complex geometries and configurations not achievable with other magnet materials.
Various Alnico alloys are achieved by modifying the chemistry and manufacturing process. These alloys can be tailored to obtain a variety of magnetic properties and characteristics. For example, specialized casting techniques are used to achieve the unique crystalline grain orientation found in the Alnico 5-7 grade.
Most Alnico produced is “oriented” and this is where the alloy’s properties are optimized by imparting an “alignment.” The alignment or orientation occurs during a heat treatment process which is unique to Alnico. The direction of orientation for most Alnico material is determined during this process which involves heating the casting or sintered part above its Curie Temperature and then cooling it at a controlled rate in the presence of a directionalized magnetic field. The actual shape of the magnetic field as well as its intensity can be optimized during this process.
Magnets which have been processed in this fashion are Anisotropic in nature and exhibit a preferred direction of orientation. Unoriented materials (Alnico 2) are available for those applications which require the specialized magnetizing capabilities of a non-aligned material. Unoriented Alnico is also typically more cost effective than oriented or anisotropic alloys.
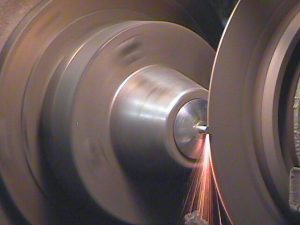
Final shaping of the Alnico materials is achieved by abrasive grinding and cutting where close tolerances are required, otherwise it is desirable to use the part with as-cast features.
Alnico magnets produced by the powder metal method lend themselves to shapes with more features. A conventional tool is required to facilitate the “pressing” operation and this can add cost, but finish machining is typically not necessary because the parts can be made to size or near net size.
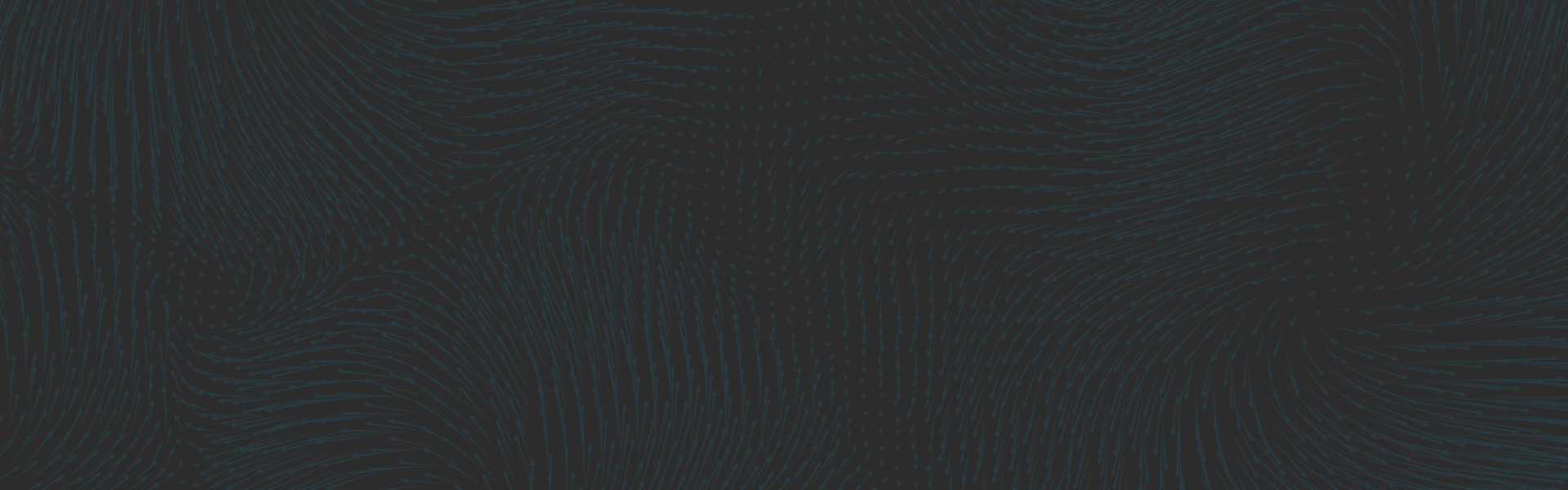
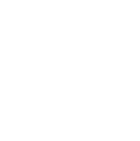
ITAR Registered & Compliant
We are registered and compliant with the International Traffic in Arms Regulations (ITAR). This qualifies us to work with items listed on the United States Munitions List (USML). We are also ITAR registered with the Directorate of Defense Trade Controls (DDTC).