Concept Validation
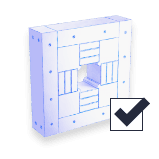
We are committed to using technology and design to ensure the manufacturability of your magnetic requests, because we understand that our customers are not always certain about the existence or feasibility of a magnetic solution.
Dura leverages its technical assets, including computer simulations with 2D and 3D FEA and boundary analysis software to validate design concepts. This helps to reduce product development time and expense, while ensuring manufacturability of the finished product. By utilizing simulation software, a tentative solution can be generated, forwarded, and discussed with your design team. After preliminary models are reviewed, an informed decision can then be made on how or whether to proceed.
Reverse Engineering
Dura’s industry expertise and in-house capabilities allow us to reverse engineer an existing magnet or magnetic assembly to improve performance, enhance service life, quantify and qualify older designs, and reduce costs.
These capabilities include:
Hysteresis Graph to Quantify Magnetic Characteristics
Simulation and Modeling
Performance Benchmarking
Chemical Analysis
Optimization for Performance, Cost, & Price Volatility
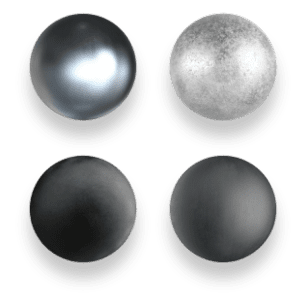
Magnet alloy is often the most expensive part of an assembly. By optimizing a magnet design for an application using simulation software, Dura Magnetics can significantly reduce the cost.
Relative to common commercial materials such as steel, aluminum, and plastic resins, the volume of magnet alloy manufactured in the world is quite low. Because of the low magnetic alloy production levels and small number of mines, refinery operations, and mills, price volatility is quite common. Using an engineering-oriented approach to design, Dura Magnetics can optimize the magnet for your application’s specific product, reducing your exposure to price volatility.
Trusted to meet your regulatory needs
Export Controlled Item
Conflict
Minerals Section 1502 Dodd-Frank
REACH
RoHS – RoHS 2
We focus on quality
MIL-SPEC 45208A tolerances
Coordinate measurement machines and video inspection system
In-house testing of field density and field strength
Hysteresis graph for magnetic characteristic measurement
Engineering & Product Development Specialists
Are you frustrated because potential vendors are not effectively communicating the nuances of a design or fabrication process? Or have you grown weary of hearing your application is too simple or too technically complex? Then perhaps it is time to consider Dura. We are an engineering-oriented company that has the willingness and ability to understand industry, segment, language, and unique specifications.
Unlike some magnet design manufacturers that limit access to design and engineering staff, Dura understands that communication is key to your project’s success. Our design and engineering team members remain engaged throughout the life of your project to ensure that a knowledgeable professional is always available. Whether your project’s scope ranges from prototype development to production quantity runs, we welcome your magnet or magnetic assembly challenges and the opportunity to provide you with best-in-industry solutions.
Contact us to get started on your next project.
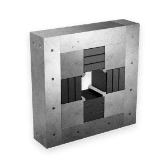
Next Step:
Custom Magnet Manufacturing
Once we’ve overcome any challenges in designing and engineering your magnet or magnetic assembly, it’s time for manufacturing.