1) What is the strongest type of magnetic material?
Neodymium iron boron magnets are the strongest magnet available with energy products up to 52MGOe available. Neodymium alloys are very susceptible to magnetic strength loss due to high temperature therefore proper consideration should be given when selection neodymium for use within an application.
Related TechTalk Articles for Further Information:
- Understanding N52 Neodymium Magnet Alloy
- Effects of Heat on Neodymium Magnets: Reversible vs. Irreversible Field Loss
2) Why don’t magnets pull forces meet what they are advertised to pull?
Most pull forces are listed under laboratory conditions. There are many factors that affect the real world pull force of a magnet. Air-gaps resulting from irregularities or paint on the work piece surface and relatively thin work piece thicknesses are some common culprits in deficient pull force measurements. Other instances including using a magnet in sheer will result in a lower than expected pull force.
3) Can magnets be soldered, welded, tapped, cut, drilled, or machined?
No, magnets typically cannot be soldered or welded. Likewise, they cannot be tapped because they are characteristically hard and brittle. It is however possible to grind, drill, or EDM magnets using specialized tools and machinery. It is also very difficult to weld around a magnet because the magnetic field biases the arc; however, magnets can be incorporated into a housing which can contain various features.
Related TechTalk Articles for Further Information:
4) How does temperature affect magnets?
All magnetic materials will lose strength at higher temperatures, however, not all at the same rate. Conversely, with many materials there will be an increase in strength at lower than ambient temperatures.
Related TechTalk Articles for Further Information:
- Alnico Magnets for High Heat Applications
- Effects of Heat on Neodymium Magnets: Reversible vs. Irreversible Field Loss
Related Tools:
5) How can magnets be damaged by impact?
All magnetic materials are relatively brittle. Magnets of varying strengths can draw ferrous objects or other magnets towards them with surprisingly high forces causing a magnet to shatter. Alnico magnetic alloys are vulnerable to magnetic loss due to poor alnico magnet handling techniques.
Related TechTalk Articles for Further Information:
6) What are the size limitations of magnets?
Magnets segments can be produced in sizes ranging from 0.020″ diameter x 0.008″ thick to 4″ wide x 6″ long x 1″ thick. Much larger magnetic assemblies comprised of many segments are possible and can be designed and built to custom specifications.
7) What dimensional features are available on magnets?
We can produce magnets with a range of features including chamfers, slots, grooves, holes, pockets, and radii of varying sizes.
Related TechTalk Articles for Further Information:
8) How do coatings and metallic plating affect the strength of magnets?
The largest factor in this is the thickness of the coating. Thick layers of paint will degrade the holding force more than thin plating.
9) What types of coatings are available?
We offer a variety of coatings including nickel, zinc, gold, parylene, and epoxy. Consult one of our magnet application engineers with your specific requirements and we can work to make a recommendation.
10) What are permanent magnets made of?
Permanent magnets are primarily made from metallic elements that can either be magnetized or are strongly attracted to a magnet. Other non-ferrous materials are sometimes added to create specific and desirable properties.
11) Do all grades of neodymium magnets need coating?
Surface treatment is recommended for sintered neodymium magnets. Their composition inherently lends itself to corrosion if it is un-coated.
12) What are the thicknesses of coatings on magnets?
Most coatings on magnets are less than 25 microns [0.001″] in thickness. Below are some thickness values for typical coating and plating options:
Thicknesses for Typical Coating and Plating Options | |
---|---|
Type | Thickness (um) |
Multi-layer (Ni-Cu-Ni) | 12 ~ 25 |
Parylene C | >7 |
Everlube | >20 |
Epoxy (E – Coat) | >5 |
Zinc | 7 ~ 15 |
13) When and why should samarium cobalt magnets be plated or coated?
Samarium cobalt magnets exhibit good corrosion resistance when compared to neodymium magnets. Plating a samarium cobalt magnet makes sense when it is working under vacuum to reduce out-gassing or to help protect the magnet from chipping. Samarium cobalt magnets should be coated when operating in an acidic environment.
14) What materials can be used to block or shield magnetic fields?
Nothing will “block” a magnetic field, but high permeability, low coercivity materials such as high Nickel based alloys are often used to shield low intensity magnetic fields. Oftentimes mild low carbon steel can be used to shield high intensity fields.
15) How is the strength of a magnet measured?
Magnetic strength is measured using devices such as pull force gauges, gauss meters, and flux meters. We can recommend the type of measurement to use based on your application’s requirements.
Related TechTalk Articles for Further Information:
16) How consistent are the magnetic properties from magnet to magnet?
Simply stated, the magnetic properties of two identically sized magnets fabricated from the same block of material should be within 1% of one another. Other important factors such as the size of the fabricated block and the specific material type and grade affect the consistency.
17) Will a magnet with a Br (residual induction) of 12,000 G mean the surface gauss will measure 12,000?
No, the Residual Induction (Br) pertains to the measurement of flux density within a closed magnetic circuit. The actual field density realized on the surface of the magnet will be much lower than the (Br) and will vary on the magnet’s pole face based on position.
Related TechTalk Articles for Further Information:
18) What is the difference between curie temperature and maximum operating temperature?
Curie temperature is the transition temperature which the magnetic alloy loses its magnetic properties. The maximum operating temperature is a nominal value given to a material grade is usually the maximum serviceable temperature of a magnet.
Related TechTalk Articles for Further Information:
19) Do permanent magnets lose strength?
Permanent magnets are materials that retain magnetic properties in the absence of an inducing magnetic field. Factors such as heat, cold, shock, or repelling magnetic fields can cause magnets to become partially or completely demagnetized. Each commercially available magnet alloy will experience these demagnetizing effects differently and for this reason there is not a one size fits all magnetic alloy solution for all applications.
20) Do neodymium magnets need to be licensed?
Neodymium magnets have an abundance of Intellectual Property rights associated with the chemistry and manufacturing process. There are many patent holders and several hundred patents enforced over most geographic regions in the world. Each country’s International Trade Commission will dictate what is considered infringing and illegal; however, the classification is not applied in a comprehensive manor. For instance, what may be legal in the US may not be legal for import into Japan.
21) Why should I use a magnetic assembly instead of a plain magnet?
It depends. Magnetic assemblies offer a variety of advantages over a plain magnet including mechanical and magnetic strength advantages. It also allows for the integration of mounting features and can protect the sensitive magnet material from damage and from corrosion. We can help you evaluate which is best for your magnetic application.
Related TechTalk Articles for Further Information:
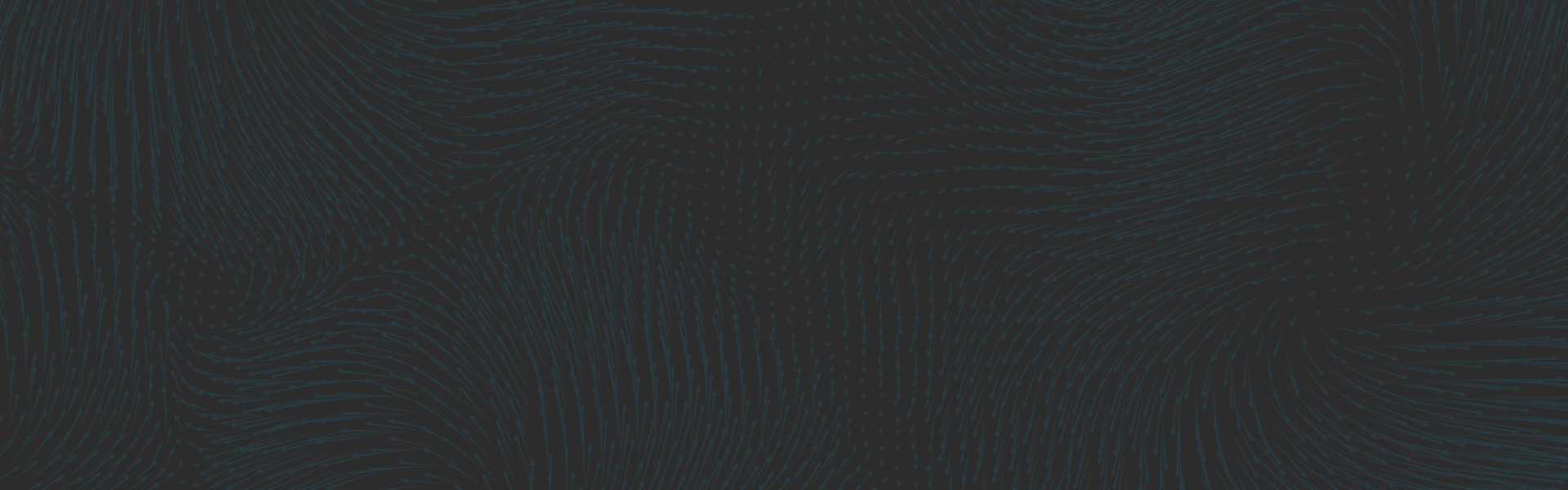
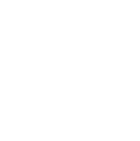
ITAR Registered & Compliant
We are registered and compliant with the International Traffic in Arms Regulations (ITAR). This qualifies us to work with items listed on the United States Munitions List (USML). We are also ITAR registered with the Directorate of Defense Trade Controls (DDTC).