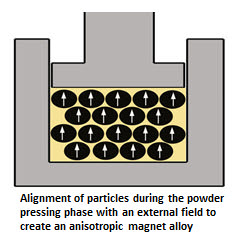
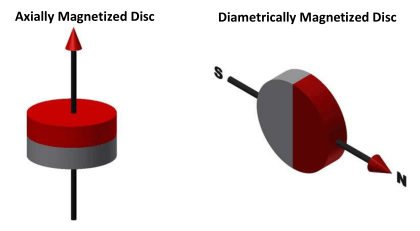
Most useful commercial magnets are anisotropic, which means that they have an “Easy” or preferred direction of magnetization and that an orientation field was applied during the compaction stage of the manufacturing process.
It is essentially impossible to magnetize the resulting anisotropic magnet alloy other than in the Direction of Orientation; however, various pole configurations can be achieved without conflicting with the magnet material’s orientation.
Below are conventional and standard industry options for the magnetization directions of Rare Earth / Neodymium Magnets.
Disc Geometry
Polarity Nomenclature: Typically the arrowhead indicates the North pole of the magnet. For symmetric geometries, indicating the location of a particular pole is unnecessary, but for non-symmetric geometries, identifying a particular pole location is very important.
Example: An axially Magnetized disc magnet does not require communication as to the NORTH pole’s position, but a radial arc does. One must indicate if the NORTH pole is to reside on the Inner radius or Outer Radius.
Block Magnet
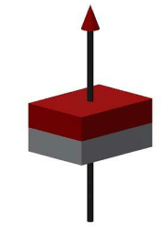
“Block Magnets” or Rectangular / Square magnets have three potential orientation directions.
The block magnet can be polarized in any direction.
Ring Geometry
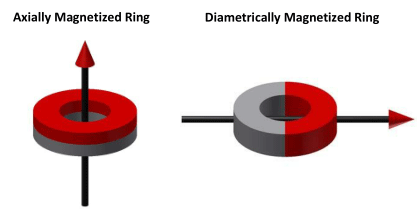
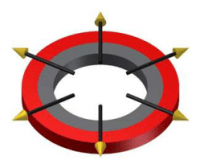
Radial Magnetization:
Radially oriented and magnetized rings are available in Neodymium Iron Boron, but there are many limitations in alloy grade, Outside Diameter/Inside Diameter ratio, axial, length, etc. Specialized tooling must be created and there is an upfront capital investment which acts as a cost inhibitor for most applications.
Radial Ring Magnetization Approximation:

Neodymium Iron Boron magnets can be approximated by arc segments; however, in most cases the magnets must be assembled magnetized and there must be a large performance benefit to the application to absorb this cost.
As with “True” radial rings, true radial Arc Segments are difficult to manufacture, but can be approximated themselves.
Arc Segment Geometry
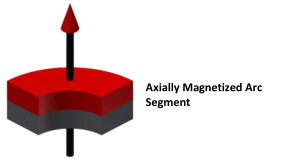
Radially IN / Radially Out:
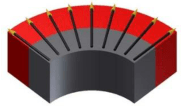
An arc segment can be polarized NORTH or SOUTH on the Outside Radius. (The resulting opposite pole will reside on the Inside Radius.)
It is very difficult to achieve a true “radial” orientation during the pressing/alignment stage of manufacturing and therefore, truly radial Neodymium Iron Boron magnet, Samarium Cobalt magnet, and Ceramic magnet arcs are rare and specialized. (An approximation of a true radial Orientated Radial Arc is widely utilized in industry.)
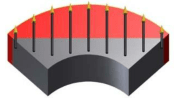
The approximated radial arc utilizes linear orientation/magnetization along a straight axis. The radial component diminishes on the leading and trailing edges of the approximated radial arc.
Circumferential:
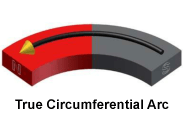
Circumferential Orientation and Magnetization is not available for Arc magnets comprised of Neodymium Iron Boron and Samarium Cobalt; however, this magnetization geometry can be approximated.
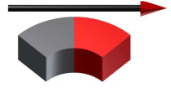
The approximated radial arc utilizes linear orientation/magnetization along a straight axis. The radial component diminishes on the leading and trailing edges of the approximated radial arc.
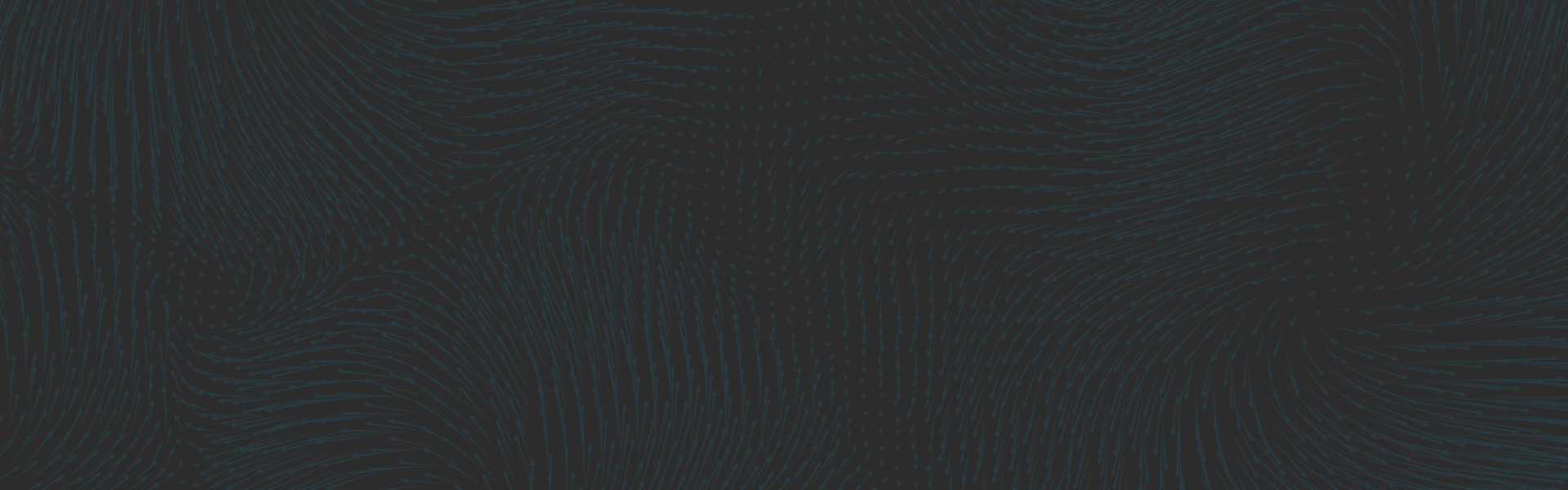
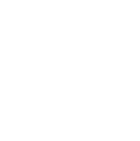
ITAR Registered & Compliant
We are registered and compliant with the International Traffic in Arms Regulations (ITAR). This qualifies us to work with items listed on the United States Munitions List (USML). We are also ITAR registered with the Directorate of Defense Trade Controls (DDTC).