There are several different magnet types, which vary depending on their makeup and magnetization, including temporary magnets and permanent magnets.
What is a Permanent Magnet?
Permanent magnets are “always on,” unlike temporary magnets. Permanent magnets are comprised of alloys of different materials, which influence the final characteristics of the magnet.
The strength of the magnet varies depending on what it is made of, as indicated by its maximum energy product value measured in Mega Gauss Oersteds (MGOe). For example, a neodymium magnet alloy might have a strength of up to 55 MGOe, while a ceramic (ferrite) magnet might have an MGOe of up to 3.8.
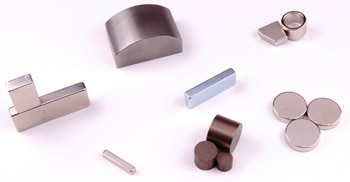
Permanent Magnet Types
Ceramic
Permanent ceramic magnets are also known as ferrite magnets. They contain sintered iron oxide and materials such as barium or strontium carbonate.
Ceramic magnets are relatively inexpensive, although they are not as strong as some other permanent magnets. They are also more resistant to demagnetization than some other magnet types.
Making ceramic magnets requires pressing and sintering. Since they can be quite brittle, a diamond wheel should be used if grinding is required.
Ceramic magnets may be isotropic grade, in which they are equally magnetic in all directions, or anisotropic, meaning they are magnetized in the direction they were pressed. The strongest ceramic magnets measure up to 3.8 MGOe, making them the weakest of the permanent magnet types.
Overall, ceramic magnets balance magnetic strength with cost-efficiency, and their tendency toward brittleness is balanced by their excellent resistance to corrosion. They have strong coercive force as well, and resist demagnetization, making them an affordable choice for common applications such as toys, crafts, and motors.
Neodymium
This rare earth magnet is incredibly strong, although brittle and subject to corrosion. Neodymium Iron Boron magnets (NdFeB) are easily oxidized because of their iron content, and they are costlier than other permanent magnet types. However, they are a very high energy product (up to 55 MGOe), with a high coercive force.
To counteract neodymium’s weak resistance to corrosion and low temperature resistance, these magnets can be coated with surface treatments, such as gold plating or resin. This allows them to be used in a variety of applications that would otherwise be inappropriate due to heat and corrosion concerns.
Neodymium magnets are frequently used in applications such as consumer electronics and healthcare and medical devices, thanks to the small sizes that can be achieved with this material.
Samarium Cobalt
Developed in the 1970s, Samarium cobalt magnets are stronger than ceramic and alnico magnets, but not as strong as neodymium magnets. There are two main groupings of samarium cobalt magnets, which are divided by energy range. The first group, Sm1Co5, (also known as 1-5), has an energy product range of between 15 and 22 MGOe. The second group, Sm2Co17 (2-17), has a range of 22 to 32 MGOe.
Samarium cobalt magnets are rare earth magnets that work well in high-temperature applications, up to 300 and sometimes even 500 degrees. This gives them a clear advantage over other permanent magnet types, which do not have as strong a temperature resistance. Nor do samarium cobalt magnets require a coating to protect against corrosion, as neodymium magnets do.
The downside to this magnet type is its low mechanical strength. Samarium cobalt magnets tend toward brittleness and chipping. However, when applications call for temperature and corrosion resistance, samarium cobalt magnets may be the most appropriate choice.
Alnico
Alnico magnets are made of a blend of aluminum, nickel, and cobalt. They may also contain small amounts of other minerals, as well, to enhance desired properties.
Alnico magnets are typically created by sintering (much like ceramic magnets) or by casting. The method of creation affects the resulting magnet, with sintering providing for improved mechanics and casting delivering higher energy.
Sintered alnico magnets are available in grades ranging from 1.5 to 5.25 MGOe, whereas cast magnets deliver between 5.0 and 9.0 MGOe. Anisotropic alnico magnets allow for customizing magnetic direction, which can be useful.
Alnico magnets can function at extremely high temperatures, which makes them ideal for stability in certain temperature ranges. They’re also quite affordable and they offer excellent corrosion resistance without the need for coatings. Plus, alnico magnets are easily manufactured into different shapes as needed.
Customizing Permanent Magnets
Because each type of permanent magnet has its own unique strengths, they can be customized to your specific needs and applications. Permanent magnets are used in applications ranging from smartphones to cars to medical imaging equipment and other precision magnetic assemblies.
The exact use of the magnet will dictate the most suitable alloy for a permanent magnet. While permanent magnets are available in stock configurations, you aren’t limited to that. Our specialists at Dura Magnetics help you determine which magnet best suits your needs, allowing you to customize your magnets down to alloy, size, geometry, finish, coating, and more.
From concept to fabrication and testing, Dura Magnetics offers outstanding technical engineering expertise in custom magnet manufacturing. We provide magnetic concept validation at the outset of your custom project, using an AS9100D multi-step process to ensure the design will meet your desired performance while optimizing the prototype and manufacturing process.
Our engineering team creates custom magnet solutions and assemblies for advanced applications, including aerospace, healthcare, robotics, and defense. During the manufacturing process, your custom magnet assembly is fabricated in-house, thanks to our standing supply of permanent magnet alloys, trained personnel, and key vendor relationships. Turnaround is quick and we strive to constantly exceed your expectations.
The custom magnet process doesn’t end there: Dura specialists provide rigorous quality management processes including testing and quality assurance. Your magnet is assured to work exactly as specified.
Dura Magnetics: Custom Permanent Magnet Experts
When your high-performance application requires custom magnets, the technical experts at Dura can help you determine the best solution for your needs and budget. Contact us to speak with our experienced team or request a quote.