Fully dense Neodymium Magnets (also known as neo magnets, neodymium iron boron, neo, or rare earth magnets) are usually manufactured by a powdered metallurgical process. Micron size Neodymium and iron boron powder is produced in an inert gas atmosphere and then compacted in a rigid steel mold or in a rubber mold. The rubber mold is compacted on all sides by fluid and is referred to as isostatic pressing. The steel molds will produce shapes similar to the final product, while the rubber mold will only create large blocks (loaves) of Neodymium magnet alloy.
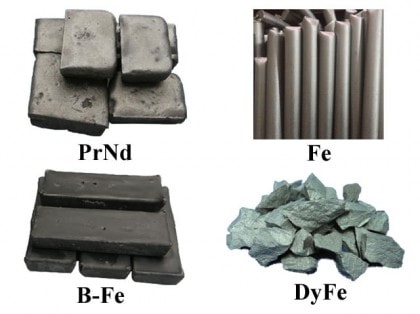
neodymium/praseodymium (PrNd), iron (Fe), boron/iron (B-Fe), and dysprosium/iron (DyFe).
The Neodymium alloy’s magnetic performance in both compacting methods is optimized by applying a magnetic field before or during the pressing operation. This applied field imparts a preferred direction of magnetization, or orientation to the Neodymium magnet alloy. The alignment of particles results in an anisotropic alloy and vastly improves the residual induction (Br) and other magnetic characteristics of the finished rare earth magnet. After pressing, the Neodymium Magnets are sintered and heat treated until they reach their fully dense condition. The die pressed magnets are ground to the final dimensions, but the brick magnets from the rubber mold method are usually squared on large grinders and then sliced to the final geometry. Isostaticly pressed alloy has higher magnetic properties than the die pressed material, but it may lack the uniformity. The choice of manufacturing method to create Neodymium Magnets is usually application driven and is typically not a concern of the customer.
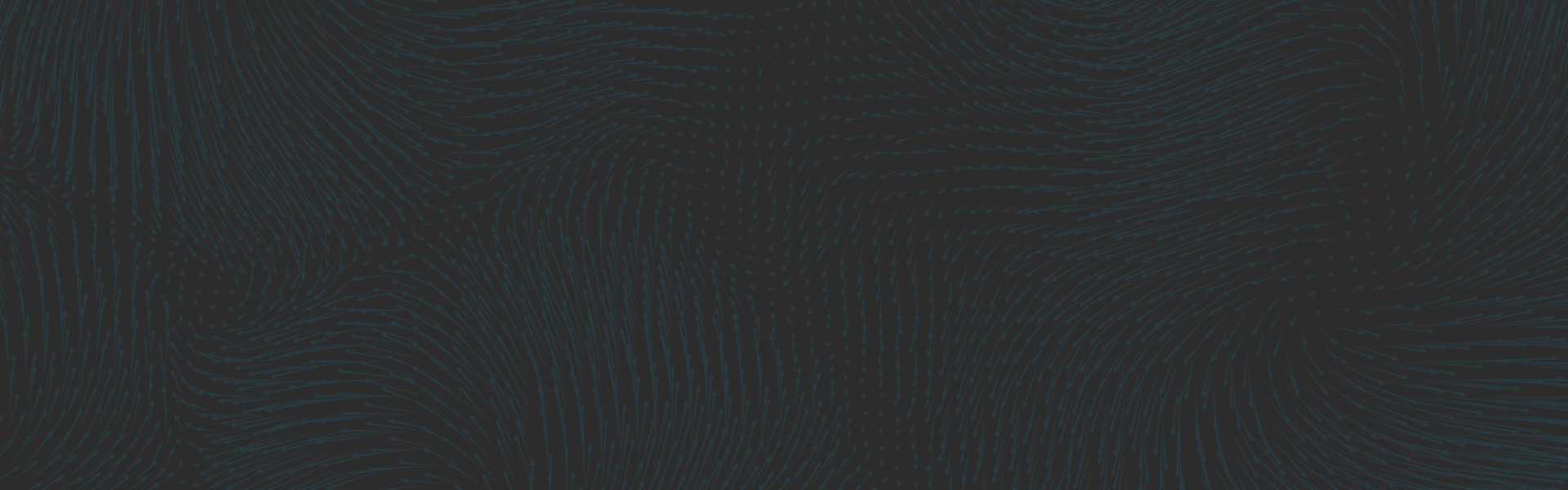
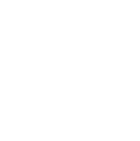
ITAR Registered & Compliant
We are registered and compliant with the International Traffic in Arms Regulations (ITAR). This qualifies us to work with items listed on the United States Munitions List (USML). We are also ITAR registered with the Directorate of Defense Trade Controls (DDTC).