In previous blogs, we have shared how to choose a magnet material and how to choose a magnet grade. The next step is determining whether to apply a coating to your magnet.
Some applications require a conformal coating or metallic plating on the magnet for trouble-free operation. A coating or plating offers protection along with numerous advantages as described in detail below.
Corrosion Protection
The most common reason to apply plating or coating to a magnet is to provide protection from corrosion. If your application is intended for use outdoors, exposed to the elements, or in a moist environment, corrosion is inevitable in an untreated magnet.
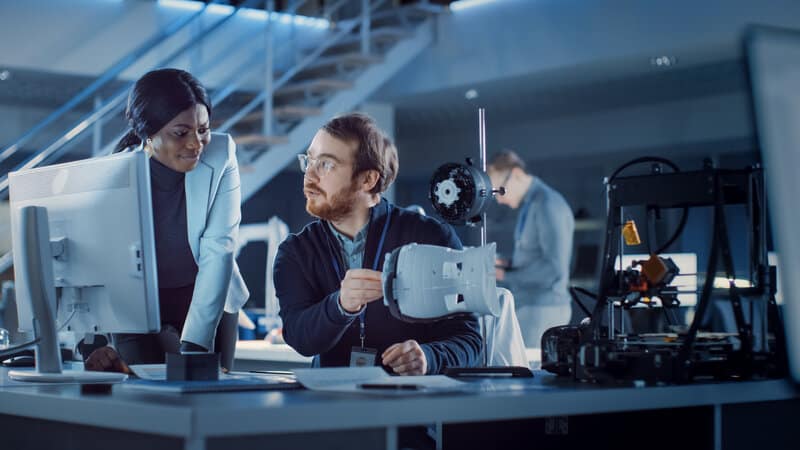
Protecting the magnetic field
Corrosion protection also prevents the reduction of the magnetic field resulting from a volume loss of the magnet alloy material. For example, Neodymium Iron Boron is highly reactive to moisture and salty environments. Other materials, such as Samarium Cobalt, are modestly reactive to moist environments and salts.
Preventing expansion
Another reason corrosion protection is important is to protect against dimensional expansion. When magnets corrode, they exhibit an oxide layer—rust—which may increase the dimensions of the magnet. Expanded size from an oxide layer can interfere with other elements in an application. For example, with a motor, rust may affect the way the rotor and the stator interact, decreasing the motion or even inhibiting the free movement of the parts.
Cleaning Ability
With the proper plating or coating, you can create an easily cleanable outer layer on the magnet. The existing production surface finish on many magnets can be insufficient for removing small particulates and can be easily stained, but the magnet plating or coating has a much smoother surface finish, allowing for more thorough removal of debris.
Magnets can attract rogue iron filings, or debris with ferrous material in it. It is easy to remove these particles when the magnet has been coated, significantly reducing the worry of surface chipping due to foreign material buildup. Coatings also prevent the sloughing of substrate materials and the release of particulates from the magnet alloy by enveloping the magnet and containing particulates.
Electrical Conductivity
The conductivity of most magnet alloys is low to moderate relative to conventional materials used for electrical connections. Adding a metallic plating affects conductivity. Certain coatings, such as gold, can increase the conductivity and improve the magnet’s effectiveness in certain applications.
Physical Integrity
Magnetic alloys can be brittle and prone to chipping and fracturing from mechanical stress and impacts. Metallic plating or conformal coating adds a layer of protection to the magnet. The best protection is found in electrolytic multilayer plating involving nickel, as nickel has double the tensile strength of a magnet alloy substrate and reduces or eliminates mechanical penetration into the magnet. Therefore, a Samarium Cobalt magnet that has been plated with nickel will require a great deal more force to break it compared to that required to break an un-plated Samarium Cobalt magnet.
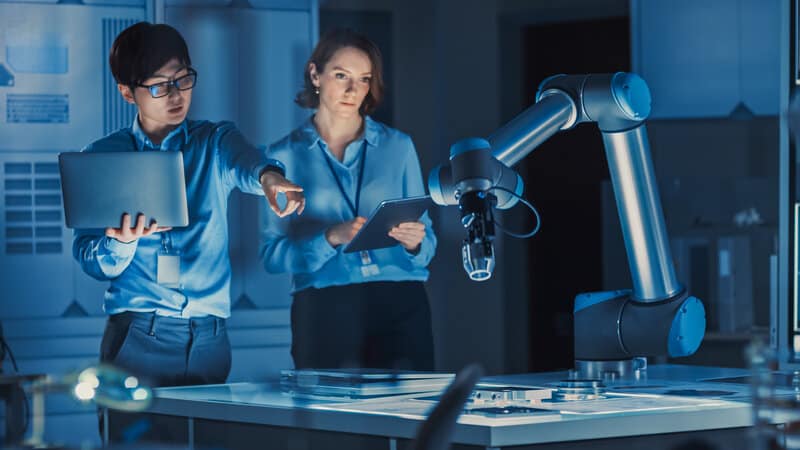
Reactivity
In certain applications, such as health care, a low reactivity coating may be desired in order to provide an inert interface between a magnet and human tissue. In the case of implants, for example, a conformal coating creates a low reactive surface. A common choice of coating is Parylene, used to encapsulate the substrate in medical applications where it is necessary to isolate the magnet from bodily fluids. Magnets used in medical equipment are typically first plated and then Parylene coated; this also helps the magnet withstand autoclave sterilization, which otherwise could cause the magnet to rust.
Outgassing
Finally, coating and plating can reduce or even eliminate outgassing, which can pose a danger to delicate equipment.
Many magnet alloys are not fully dense, as they are fabricated by compressing powdered metal in a process called sintering. This leaves the magnets semi-porous and vulnerable to trapped moisture, chemicals, and atmospheric gases. When integrated into your application, the magnet could outgas these materials, causing contamination or interfering with correct operation.
Sensitive equipment can rarely tolerate contamination, so a coating is used to prevent outgassing. For example, a magnet used in optics lasers can be plated in nickel and encapsulated in Parylene to separate the magnet alloy matrix from the vacuum.
Your Magnet Plating and Coating Partner
As you explore the best materials for plating and coating a magnet for your particular application, we at Dura Magnetics are eager to help. Our customers lean on our years of experience to find the best plating and coating solutions. We help you understand the working environment of your magnet application, using our multi-industry expertise, and direct you to the solution that will best fit your performance and budget requirements.
Contact us to develop your custom magnet solution. Our magnet engineers will consult with you about your design and help you create the ideal solution.