After identifying the material best suited for your magnet or magnetic assembly, the next step is to determine the specific grade of material needed for your application.
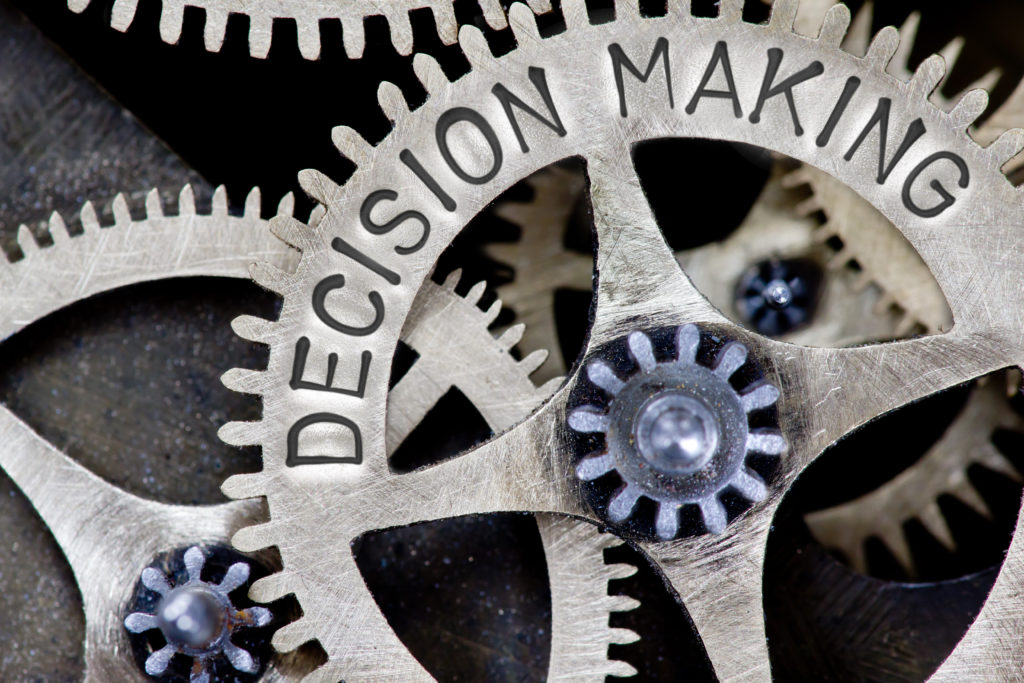
For Neodymium, Samarium Cobalt, and Ceramic materials, the grade is an indicator of magnet strength: the higher the material grade number, the stronger that magnet. Alnico is a notable exception to this rule. The size dependent nature of Alnico means grade will not always correlate with strength.
Choosing the proper material grade will have far-reaching implications for the performance of your product. At Dura Magnetics, we utilize our years of experience to help you make the right choice. Below are some factors to consider when selecting the material grade for your application:
1. Maximum Operating Temperature
Maximum operating temperature is a primary factor in determining which magnet material to choose; it is just as important when determining the grade of that material. Magnets are incredibly sensitive to fluctuations in temperature, so it is critical to have your operating temperature range defined prior to selecting your grade.
At Dura Magnetics, we simplify this process for our customers by grouping our available materials by operating temperature. This is especially valuable for Neodymium, which has a diverse selection of operating ranges. You can view our available magnet materials grades for Neodymium, Samarium Cobalt, Ceramic, and Alnico. Not all material grades are available for every temperature range.
2. Required Magnetic Field Density or Holding Force
When determining the required magnetic field density or holding force, we offer a word of caution — don’t select a higher grade than what you may actually need. Why design with 52 MGOe Neodymium, when 45 MGOe Neodymium will suffice? While it may be tempting to choose the highest strength material grade, it may not work within your intended application. For example, N55 (55 MGOe Neodymium) offers high strength, but risks demagnetizing in high temperature applications. Choosing a higher grade than what you may need could also be unnecessarily expensive, particularly if you’re designing for a high-volume consumer application.
At Dura Magnetics, we make it simple for customers to determine the material grade needed for their required field density or holding force with our two easy-to-use online calculators:
If you’re designing for a holding force application, these calculators will allow you to adjust your parameters to determine the grade, shape, diameter, and thickness you need.
3. Demagnetizing Resistance
A final consideration when choosing a magnet grade is the demagnetizing resistance. This factor will likely have a large impact on your final design. Your maximum operating temperature is directly correlated with the intrinsic coercive force (HCI) of the material. HCI is the resistance to demagnetization. The higher the HCI, the higher your operating temperature. While heat is the major contributor to demagnetizing, it is not the only factor. Magnetic fields produced in your system and the geometry of your part are other key factors for demagnetizing resistance. Once demagnetization occurs, the damage is often irreparable.
We offer a tool to help you calculate demagnetizing resistance against several variables:
Use this calculator to choose a potential design path based on your magnet grade, shape (Pc), and temperature.
How Dura Magnetics can help
At Dura Magnetics, we work closely with you to select the proper material grade and get a better understanding of your intended application. At the onset, our discussions center on two key questions: What is your operating temperature? In what environment will your magnet be used? Answering those two questions will help refine our recommendations.
If you’re designing a magnet for a circuit, meaning it will be around other materials that conduct the magnetic flux, there are many variables that must be considered. In this instance, we will create a 2D or 3D model to help determine which grade of material to use.
Choosing the right material grade at the onset of your project will make a significant impact in both cost and potential redesign time. At Dura Magnetics, we can help guide this process — ultimately saving you time and money — and resulting in the ideal magnet for your application.