How Does Heat Affect Magnetic Performance? Irreversible vs. Reversible Loss
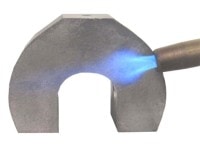
A casual review of the technical data accompanying Neodymium Iron Boron magnets reveals potential heat issues. Upon further examination of the documentation, one can observe a recommended maximum operating temperature, but with a caveat which qualifies the maximum operating temperature relative to the geometry of the magnet. It is not a hard number and will vary depending on the magnetic circuit in which the magnet is operating. This maximum operating temperature is important, but it is simply the point beyond which the magnet will experience an irreversible loss in net magnetization. Heating a magnet will cause loss of net magnetization immediately. This loss is called “reversible” as it is recovered as soon as the magnet cools back down. (Conversely, a magnet will gain net magnetization as soon as it is cooled down.)
Impact of Reversible Loss
At first glance, the irreversible loss seems to be the largest issue, but the reversible loss can cause a negative impact on a magnet’s performance because while the magnet does not permanently demagnetize, it may not generate enough field for a desired application at a particular operating temperature.
Magnetic Temperature Coefficients
To evaluate the performance of a magnet while exposed to heat but operating below the point of irreversible loss, one can estimate the impact with the magnet’s temperature coefficients; a (Br) for the Residual Induction (Br) and a (HcJ) for the Intrinsic Coercive Field Strength (Hci = HcJ). Most magnet vendors will list these values, but there is generally little application knowledge offered. (These coefficients are also typically offered as a general value, but they are actually quite different for various Intrinsic Coercive Field Strength values.) The Temperature Coefficients represent the percent change in the relevant magnetic characteristics (Br or HcJ) per degree C.
Use of Temperature Coefficients
The temperature coefficients facilitate the calculation for the loss of Br and HcJ for a magnet. The coefficients and the resulting change in Br and HcJ is treated as a linear function between a specified temperature range. This range is usually between 0°C and 100°C. Outside this range the function is considered non-linear and the coefficient method of calculating magnetic field degradation cannot be trusted. (Coefficient calculations should be considered first order and verified empirically.)
When Should Temperature Coefficients be Utilized?
For work-holding and field density applications, only the Residual Induction (Br) Temperature Coefficient will be used. The Intrinsic Coercive field strength (HcJ) Temperature Coefficient is normally used when there is an external demagnetizing field, but that is outside the scope of this article.
Limitations of Temperature Coefficients
As listed in other Dura Magnetics’ knowledge base articles, the Residual Induction (Br) is the “closed circuit” maximum induction for the magnet. This magnetic characteristic is volume independent and most magnets do not operate at this point. The magnet will typically operate at some point below the Br and so calculating the degradation of the Br does not directly translate into the Induction Operating point (Bd) of the magnet, let alone a specific field density or attractive force.
Practical Application of the Residual Induction (Br) Temperature Coefficient
The equation for calculating the resulting Residual Induction (Br) at various temperatures is listed on Dura’s Material pages. We also offer an interactive demagnetization / permeance coefficient (Pc) tool. As stated above, calculating the resulting degradation of the Br is insufficient for specifying the exact impact on an application; however, it can be used to estimate the impact.
Consider the following geometry:
- Grade 45M Cylindrical Neo magnet
- 0.500″ OD x 0.500″ thick (M)
- Work-piece 3/8″ thick 1018 mild steel
- 0.005″ gap between the magnet and work-piece
The Residual Induction and the Maximum Energy product ((BH)max) were calculated for each temperature listed below in Table 1 and a 2D FEA simulator was used to resolve the Attractive Force (lbf.) for each case.
What becomes apparent is that the Energy Density (Grade) drops considerably as the magnet is heated up. The grade 45 essentially becomes a grade 38.7. This loss is reversible and the magnet will recover, but the application may be in jeopardy as the net field of the magnet degrades. What else is apparent is the magnet loses a full two pounds of attracting force when going from 20°C to 100°C.
If the attractive force dropped then so did the net magnetic field output of the magnet. If this magnet was being used in a sensor application, the magnet may not produce enough field to operate the sensor at an elevated operating temperature.
Operational Temperature (°C) | BHmax -Grade- (MGOe) | Residual Induction (Br) (Gauss) | Change in (Br) (%) | Attractive Force (lbf.) | Incremental Change in Attractive Force (%) |
20 | 45.0 | 13,650 | 14.67 | ||
40 | 43.3 | 13,410 | -1.79 | 14.12 | -3.75 |
60 | 41.7 | 13,170 | -1.82 | 13.62 | -3.54 |
80 | 40.2 | 12,980 | -1.86 | 13.12 | -3.67 |
100 | 38.7 | 12,690 | -1.89 | 12.64 | -3.66 |
Correlation
The exercise suggests that the degradation of the magnetic field, and therefore the attractive force of the magnet, is proportional to twice the degradation of the Residual Induction (Br). This is a good first order estimate and it can be used, but should be validated empirically.
Summary of Heat and Magnetic Holding Power:
- Even though a selected grade of magnet does not experience an irreversible loss (i.e. permanent demagnetization) when heated up, it will still lose net magnetic field.
- For recoverable losses due to heating, a magnet will recover when cooled back down.
- Even though a magnet did not experience an irrecoverable loss, the recoverable loss may be such that the magnet fails to deliver adequate field at an elevated operating temperature.
- The Residual Induction Temperature Coefficient α (Br) can be used to estimate the degradation of the Br for a specified temperature range.
- The resulting percent decrease in attractive force or net field is proportional to 2 times the percent degradation of the Residual Induction (Br).
- Selecting a higher heat tolerance grade may not solve the problem of reversible field losses due to heat. A higher heat tolerance will mean that the magnet will not experience an irreversible loss at higher temperatures. This does not mean the percent loss of Br per degree C will be improved to the point the magnet will be successful in the application. The solution may be in the magnetic geometry design or changing alloys.