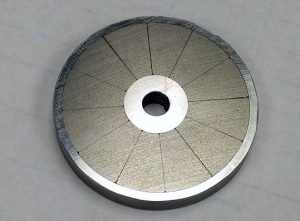
When you combine Dura’s accumulated knowledge and experience with new innovations and technology you get the best Samarium Cobalt Magnet and magnetic assembly design and engineering assistance available in the marketplace. Dura utilizes 2D and 3D magnetic simulation packages to design engineered-to-order Samarium Cobalt (SmCo) magnetic assemblies and magnet solutions for a wide range of applications, including:
- Medical Devices and Equipment
- Aerospace and Defense Programs
- Magnetic Sensor Triggering
- Thin Film Deposition and Magnetic Annealing
- Metal Working
- Fixturing and Work-Holding
- Electro Mechanical Devices
- Various Holding Applications
- Various Material Handling Devices
- Toque and Linear Couplers
Commitment to Technology and Design for Manufacturability
Customers are not always certain about the feasibility of a magnetic solution. Dura leverages available technical assets, including computer simulations with 2D and 3D FEA and Boundary analysis software to validate design concepts, thereby reducing product development time and expense, and ensuring manufacturability of your Samarium Cobalt Magnet or Magnet Assembly. Utilizing simulation software allows us to generate a tentative solution that can forwarded and discussed with your design team. After preliminary models are reviewed, an informed decision can then be made on how or whether to proceed.
Samarium Cobalt Magnet Reverse Engineering
Dura’s industry expertise and in-house capabilities allows us to reverse engineer an existing Samarium Cobalt Magnet or Samarium Cobalt Magnetic Assembly to improve performance, enhance service life, quantify and qualify older designs, and reduce costs. These capabilities include:
- Vast accumulated knowledge base
- Hysteresisgraph used to quantify the magnetic characteristics of the magnet
- Simulation Software
- Performance benchmarking of the application
- Chemical analyses
Samarium Cobalt Magnet Design Pitfalls
During the design phase, it is important to consider the complexities associated with designing with magnetic materials. Not only is the magnetic performance of the magnet important, but also how your Samarium Cobalt Magnet is integrated into the final solution.
Samarium Cobalt magnetic materials, unlike common commercial materials that have ASTM classifications, are difficult to manufacture and fabricate and present a special set of challenges. Therefore, the design team must take special care when creating a custom solution for your application. Common design challenges with SmCo Magnetic Materials include:
- Are typically environmentally unstable (highly reactive and prone to oxidation). Common coating and plating solutions usually do not translate to magnetic alloy.
- Will gain or lose magnetic field relative to the operational temperature fluctuations necessitating the need to design for magnetic performance through a temperature spectrum.
- Can experience irreparable harm at extreme temperature exposures. This harm is irrecoverable and represents an effective partial or total demagnetization of the magnet.
- Challenging to fabricate because conventional machine tools and machining methods are not feasible.
- Challenging to design because the magnetic field density and resulting force are not linear relative to distance.
- Magnetic fields can create hazards for personal and some electronic equipment.
- Common methods of component integration and retention such as; tapped holes, shoulders, through holes, staking, and tapers are expensive to employ. The integration of a magnet into a sub-assembly requires a functional knowledge base when designing an integration scheme.
- Are MAGNETIZED. This seems obvious, but magnetized magnets and sub-assemblies present a unique set handling and integration problems. The issue can range from protecting the operators to demagnetizing of the magnet itself. This aspect must be accounted for early in the design phase.
Commonly requested specifications associated with aluminum, steel alloys, plastic, etc., are usually challenging to implement with Samarium Cobalt Magnets and Samarium Cobalt Magnetic Materials. These specifications, usually indicated on a drawing by default, may add cost and complexity when manufacturing a magnet or magnetic assembly. It is important to review the relevance of these industry standard features and specifications when designing and specifying a magnet or magnetic assembly.
Click here to view a list of common, mistakenly applied, drawing attributes.
Optimization for Performance, Cost, and Price Volatility
Oftentimes the Samarium Cobalt Alloy is the most costly part of an assembly and optimizing the magnet volume used yields financial savings. By optimizing a Samarium Cobalt Magnet design for an application using simulation software, Dura Magnetics can achieve significant cost reductions. Relative to common commercial materials such as steel, aluminum, and plastic resins, the volume of Magnet Alloy manufactured in the world is quite low. Because of the low magnetic alloy production levels and small number of mines, refinery operations, and mills, price volatility is quite common. Using an engineering oriented approach to design, Dura Magnetics can optimize your Samarium Cobalt Magnet for your application, reducing your exposure to price volatility.
Special Requirements
- DFAR (Specialty Metals Clause 252.225.7009)
- Export Controlled Items
- Conflict Minerals – Section 1502 Dodd-Frank
- REACH – RoHS – RoHS 2 – RoHS 3
Quality Management System (QMS)
- Mil-Spec 45208A
- AS9100D Certification
- Coordinate Measurement Machines and Video Inspection System
- Magnetic testing equipment for measurements of Field Density and Field Strength
- Hysteresisgraph for magnetic characteristic measurement
- Variety of associated equipment for Electronic and Magnetic Performance evaluations
Custom Samarium Cobalt Magnet Engineering and Product Development Specialists
Although some magnet manufacturers limit access to design and engineering staff, Dura understands that communicating with your engineering staff is the key to every project’s success. Our design and engineering team members remain engaged throughout the life of your project to ensure a knowledgeable professional is always available to discuss project details.
If you are frustrated by poor communication and the complexities of the custom Samarium Cobalt Magnet design or fabrication process, or if you have grown weary of hearing your application is too simple, or too technically complex, then perhaps it is time to consider Dura Magnetics. We are an engineering-oriented company that understands your industry, segment, language, and unique specifications.
Whether your project’s scope ranges from prototypes to production quantity runs, we welcome your custom Samarium Cobalt Magnet challenges and the opportunity to provide best-in-industry solutions. Ready to get started? You can contact Dura by e-mail or call us at 1-800-492-7939.
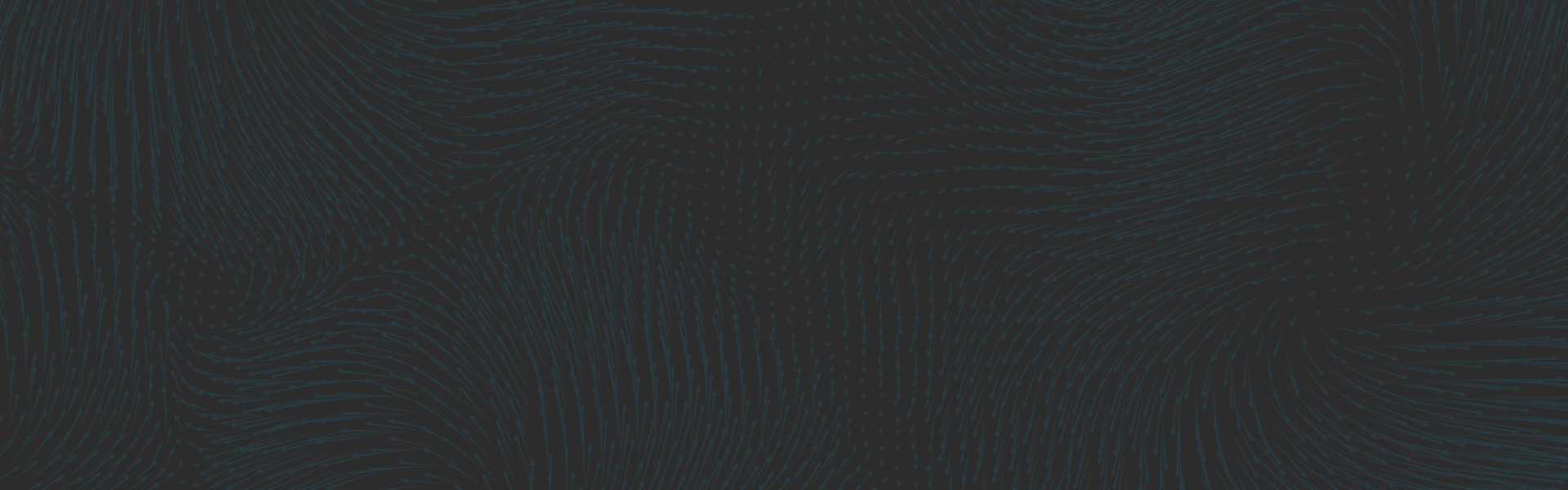
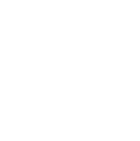
ITAR Registered & Compliant
We are registered and compliant with the International Traffic in Arms Regulations (ITAR). This qualifies us to work with items listed on the United States Munitions List (USML). We are also ITAR registered with the Directorate of Defense Trade Controls (DDTC).